
Reattach the fan using x2 self-tapping screws. Make sure to check if the square nuts are still in place as you will have to undo the assembly later if one is missing at this stage.ĩ. Reattach the heatsink and fasten the two M3 x 20 screws. You may need to apply a little pressure on the idler arm to make sure the drive gear is seated correctly.Ĩ. Insert the new drive gear into the sink, ensure the bearings are pressed onto the shaft. To make this step easier ensure the tension is set to it's the lowest setting otherwise you will be fighting against spring pressure unnecessarily.ħ. Two views A and B are shown above, they represent the same step from two different viewing angles. Make sure to locate the spring in the channel highlighted in B. Although E3D Hemera is designed to be used as a direct extruder, it can also be. Slide the idler assembly back onto the dowel pin in the heatsink, if the dowel pin is in the motor side remove it and reinsert it into the sink. Now you can unscrew the HE fan, and the 2 screws holding the housing of the gears. If the TC is powered on, the HE Fan will start to spin for reading -273 degrees.

Press the idler hobb back into the idler gear making sure that hobb section is on the same side as the short pin housing.Ħ. 1 As I have many problems with the Hemera's, some tips from my side: To fix a clog, just release the heater cartridge cable and Thermistor cable with the snap connector. Pop the Idler Hobb out of the Idler, using an Allen key, or small screwdriver to provide a lever-action makes this easier.ĥ. Was determined to not let that happen again, so i designed this fanguard for the AIO version of ChipCEs excellent Hemera mount. You will find it easier to complete this step with the idler tension set to it's lowest setting.Ĥ.

Remove the x2 M3 x 20 heatsink screws, this should allow the heatsink to be removed from the motor. Undo the x2 self-tapping screws that fasten the fan and it should pull away from the heatsink.ģ. If you try this while still at temperature you will risk serious burns.Ģ. Unscrew the HotSide from the main body.Įnsure that the unit has completely cooled down to room temperature before attempting this. Replacement drivetrain gears can be purchased hereġ. First step in disassembly: get the two hex bolts out Two mounting holes on all sides The bolts that hold the H2 together are accompanied by split lock washers which are supposed to prevent the bolts getting loose (not if you ask NASA) After the bolts are removed, the two parts that make up the direct drive extruder assembly can be pulled apart. When you remove the front panel, the filament, the tension pulley and the spring become a clean unit.Before you begin it's important to mention that you should try to avoid dropping the gears or removing any grease before assembly.
Hemera disassembly full#
Full access allows parts to be cleaned and replaced even when filament is loaded. If you need to disassemble Hemera for maintenance, you can easily access the internal mechanisms by removing the fan and loosening the two screws on the front panel. The filament tension is increased by turning it clockwise and reduced by turning it counterclockwise. To adjust the filament tension, the user simply turns a knurled screw and a cam slide mechanism with a captive nut compresses a spring and loads the tensioning pulley. The interaction with Hemera is from above. The design of the Hemera heat sink ensures that airflow is directed up and away from both the Hot end and the heated bed, reducing the risk of warping and uneven tension in the printed part.
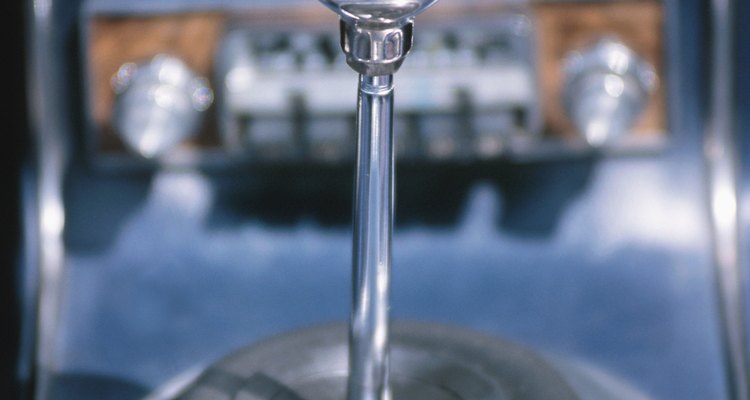
Hemera offers practical T-slots for easy mounting on your printer as well as space for additional accessories, part fans and bed levelling probes. This exceptional system also has a significant impact on the printing of rigid and semi-rigid materials such as PLA or nylon. Only when you print ultra-flexible materials can you experience the full extent of filament delivery and reliability. Hemera extrudes filaments like no other extrusion system.

Hemera disassembly install#
to install slots and produce a very compact system.įilament extrusion like no other extruder It has a custom motor based on a NEMA17, as well as its own faceplate design, which allows the user to be more comfortable, e.g. The secondary gear shaft is located on a movable, sprung idler wheel that allows the user to adjust the filament tension.Į3D Hemera is a system of components that work together seamlessly as a single compact product. Undo the x2 self-tapping screws that fasten the fan and it should pull away from the heatsink. In fact, filaments can be pushed with up to 10 kg of force. It combines the market-leading V6 hot end with a brand new filament drive to create a responsive direct drive extrusion system that offers unprecedented performance with flexible filaments.įor E3D Hemera, E3D opted for a dual drive arrangement made of hardened stainless steel, which offers enormous grip compared to single drive systems. The E3D Hemera - formerly Hermes - is the best extrusion system that E3D has ever manufactured.
